Nonwoven fabrics are the backbone of modern filtration technology, offering unparalleled strength, adaptability, and performance. Designed to remove particulate contaminants from gas or liquid, these advanced materials are produced using cutting-edge spunlaid, drylaid, and wetlaid processes. Their versatility makes them indispensable across industries, from healthcare to automotive and beyond. Let’s explore the innovative processes and technologies behind our nonwoven fabrics and their diverse applications.
Spunlaid process: Pioneering strength and reliability in nonwovens
The spunlaid process is a cornerstone of nonwoven production, extruding thermoplastic polymers into continuous filaments that are bonded to create strong, durable fabrics. This process ensures consistency and reliability for a wide range of applications, leveraging technologies like spunbond, meltblown, and electrospinning.
Spunbond technology: The foundation of durable filtration
Our spunbond technology forms the foundation for high-strength nonwoven fabrics, used as coarse filtration materials or as base layers in composite filters. These fabrics provide structure and support for finer filtration materials like meltblown layers.
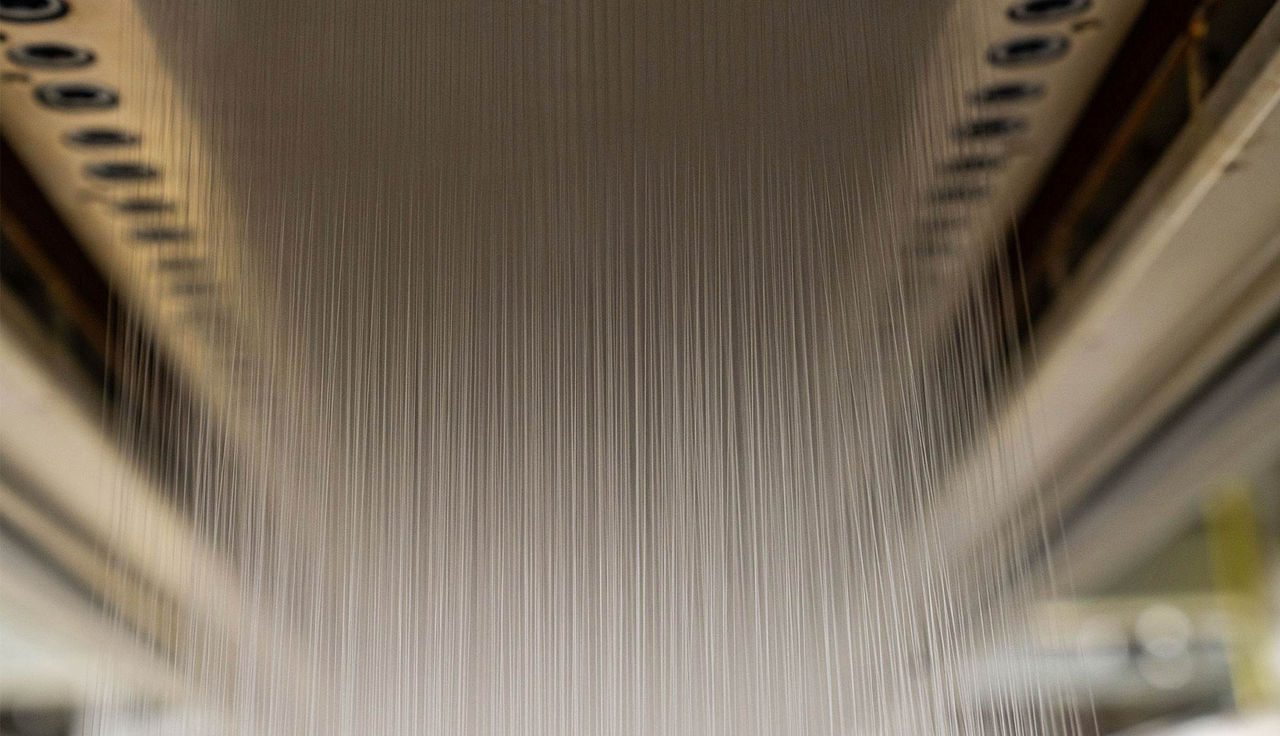
- Polypropylene (PP) or polyester (PET)
- High tensile strength for exceptional durability and reliability.
- Uniform structure to ensure consistent filtration performance across applications.
- Adaptable material properties, making it suitable for a wide spectrum of industries.
- Transportation filtration: High-efficiency filters against fine dust for cabin air and engines
- Air filters for HVAC systems: Covers filter classes ISO coarse 50 % to ISO ePM10 65%, ensuring improved indoor air quality.
- Protective clothing and masks: Provides the necessary strength and flexibility for safety equipment.
- Geotextiles: Supports construction and agricultural projects by offering robust, long-lasting materials.
Meltblown technology: High efficiency filtration at its best
Our meltblown technology delivers ultra-fine fibers (1-5 microns) to produce lightweight, flexible, and highly efficient filtration materials. Often paired with spunbond layers, our meltblown media plays a vital role in composite filters for advanced applications.
- Ultra-fine thermoplastic polymer fibers, primarily polypropylene (PP)
- Superior filtration efficiency capturing fine particles with ease.
- Lightweight and flexible material for ease of use and adaptability.
- Versatile applications, from healthcare to industrial filtration systems.
- Transportation filtration: High-efficiency filters against fine dust for cabin air and engines
- High efficiency HVAC filters: Includes applications such as HEPA filters, covering classes ePM1 to ePM2.5.
- Medical face masks: Meets the stringent requirements of healthcare environments.
- Industrial filtration systems: Ensures cleanroom standards and supports advanced manufacturing processes.
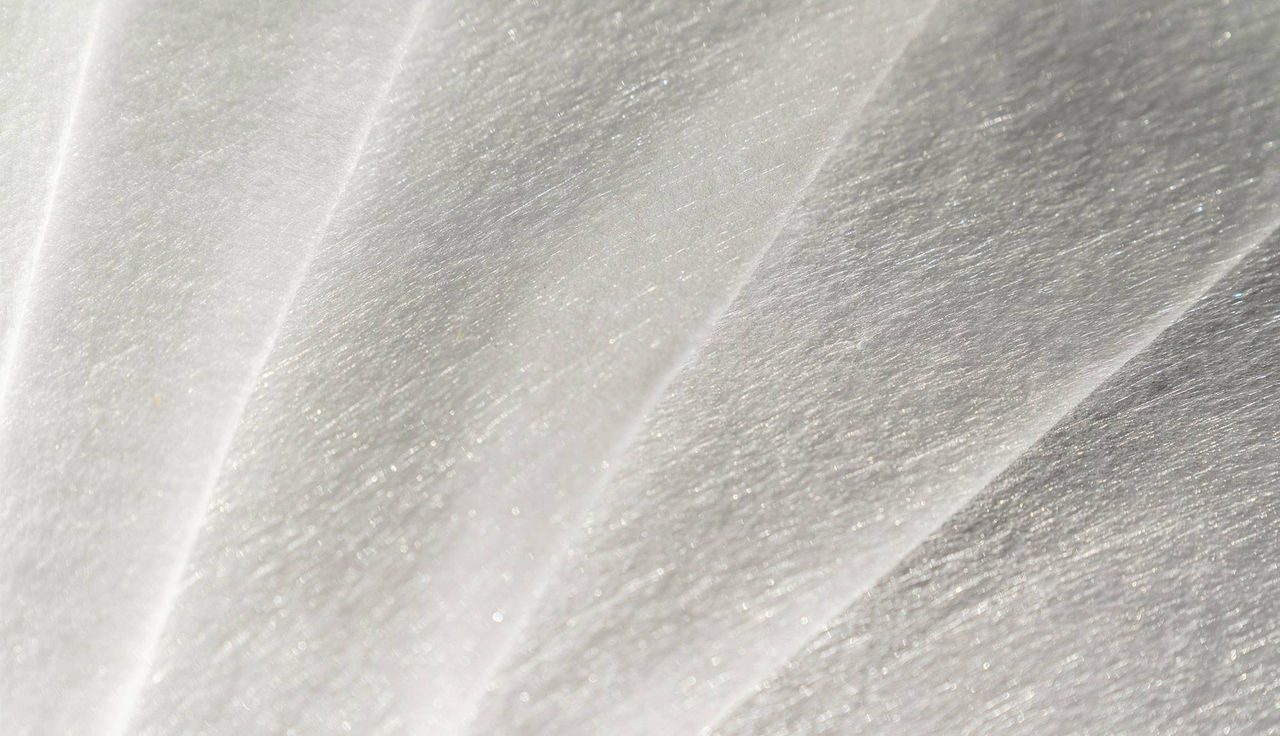
Nanofiber technology: Advanced filtration for submicron particles
Our electrospun nanofiber layers, as thin as 100 nm in diameter, enable the capture of submicron particles like fine dust as well as the mechanical filtration of aerosols. These advanced materials combine high filtration efficiency with low-pressure drops to optimize energy efficiency.
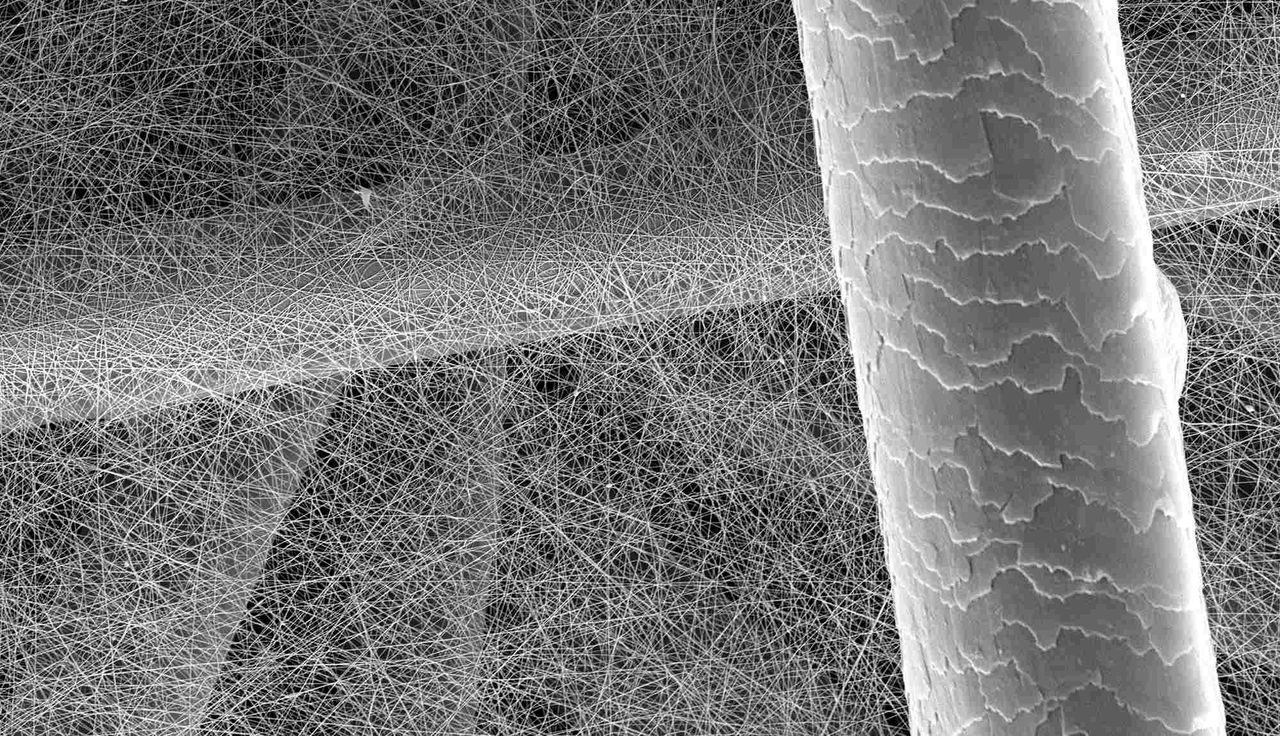
- Thermoplastic polymers such as Nylon 6 (PA6)
- Exceptional particle capture efficiency for submicron contaminants.
- Low-pressure drop to optimize energy consumption and airflow.
- Extended filter lifespan due to enhanced dust-holding capacity.
- High-performance air filters: Suitable for ePM1 to HEPA/ULPA classes.
- Automotive cabin and engine filters: Provides air and customized liquid filtration to protect people and engines.
- Medical filtration: Used in ventilators, masks, and other critical healthcare equipment.
- Industrial filtration: Captures fine particles in manufacturing and cleanroom environments.
Drylaid process: Tailored solutions for diverse needs
The drylaid process blends staple fibers into a uniform web, creating nonwoven fabrics that are durable, adaptable, and high-performing. Using techniques like carding and air-laying, this process enables the production of high-loft and versatile materials for filtration applications. It enhances the media with electrostatic features which improves its ability to capture fine particles.
Carding technology: Precision crafting for advanced filtration media
Carding technology plays a crucial role in forming nonwoven webs, using staple fibers that undergo processes such as carding, cross-laying, needle punching, and thermobonding. These techniques allow for the creation of materials with tailored characteristics, making them highly suitable for a variety of filtration applications.
- Needle punching: This process enhances filtration efficiency by creating a dense, interconnected fiber structure.
- Thermobonding: By utilizing PET and bi-component fibers, thermobonding produces durable, high-loft materials with excellent pleatability. These features make the resulting nonwovens ideal for demanding environments, such as HVAC and automotive systems, where longevity and performance are critical.
- Polypropylene (PP), polyester (PET) or acrylic fibres (PAN)
- Blended with bi-component fibers for added durability and flexibility
- Customizable filter media: Supports varying weights, stiffness, and air permeability requirements.
- High-loft structures: Progressive depth designs ideal for prefilter applications requiring enhanced dust-holding capacity.
- Robust durability: Pleatable and resistant to wear for long-lasting performance.
- Electrostatic efficiency: Consistent electrical charge of our tribo charged media enhances particle capture.
- Tailored solutions: Competitive pricing combined with specialized R&D capabilities.
- Cabin air filters: Combines high filtration efficiency with user comfort.
- Pocket filter media for HVAC systems: Covers ISO Coarse 70% to ePM10 70%
- Pleated panel media: Suitable for industrial and automotive air filters.
- Medical face masks: Meets the stringent requirements of healthcare environments.
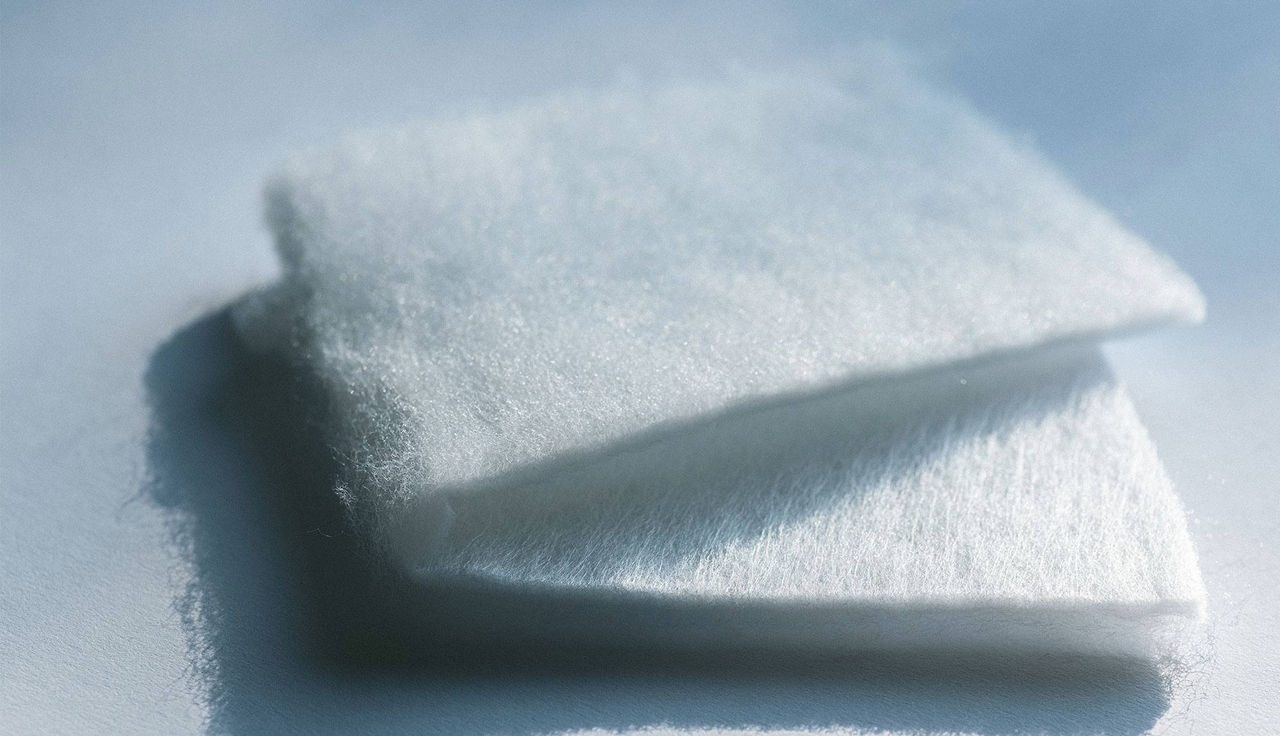
Wetlaid process: Precision and efficiency for critical applications
The wetlaid process is a sophisticated manufacturing method that creates isotropic nonwoven webs with consistent pore structures. By combining cellulose and glass fibers with synthetic fibers and additives, this process produces highly uniform and efficient materials specifically designed for critical filtration applications.
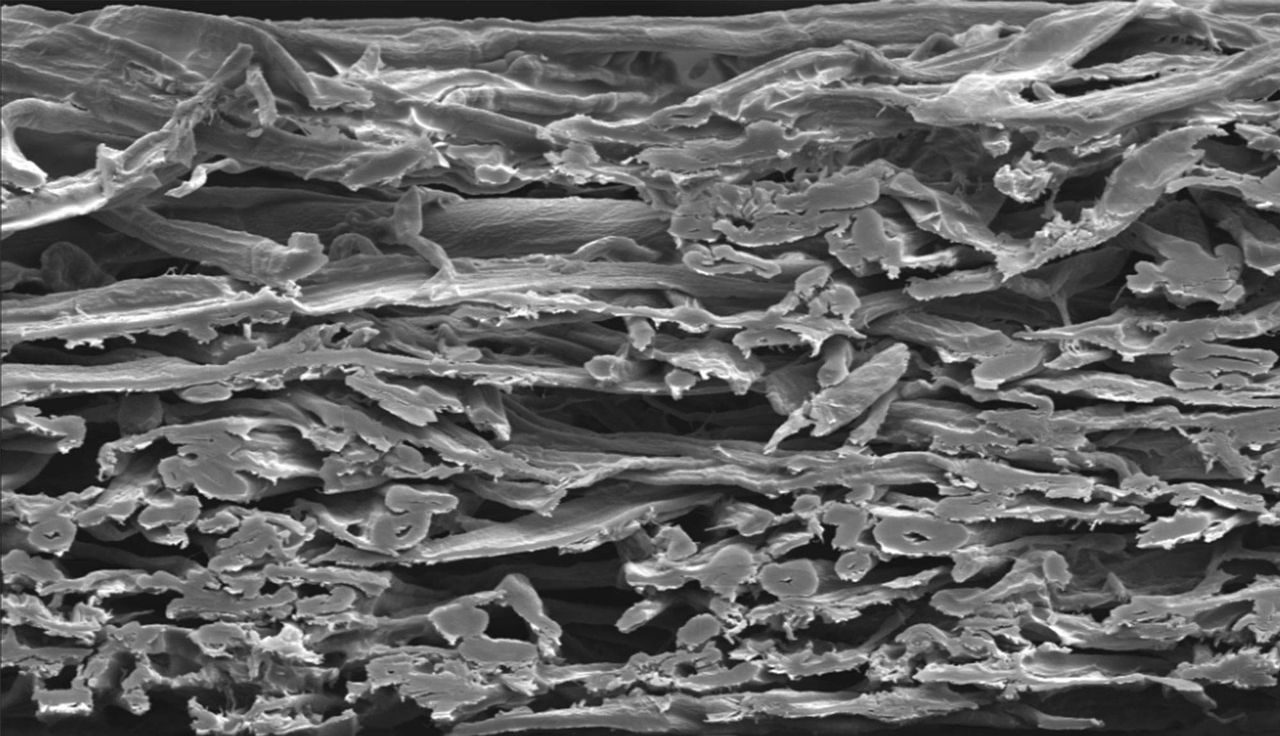
- Cellulose or glass fibers mixed with synthetic fibers based on application needs
- Fully synthetic fibres
- Customizable material design: Tailored fiber blends to meet filtration needs.
- High air permeability: Low-pressure drop for optimized energy efficiency.
- Enhanced durability: Pleatable materials that withstand demanding conditions.
- Automotive and industrial filtration: Provides extended filter life through exceptional dust-holding capacity
- Engine air filtration: With flame retardant properties.
- Fuel, oil and hydraulics filtration: Provides chemical and thermal resistance.
Nonwoven fabrics for a cleaner, safer world
Nonwoven fabrics are the driving force behind cutting-edge filtration technologies. From spunlaid strength to drylaid adaptability and wetlaid precision, these materials ensure efficient performance across industries.
As innovation continues, nonwoven fabrics will remain at the forefront of sustainable and effective filtration solutions at MANN+HUMMEL. Let’s work together to shape a cleaner, safer, and more efficient future. Get in touch with our experts now!