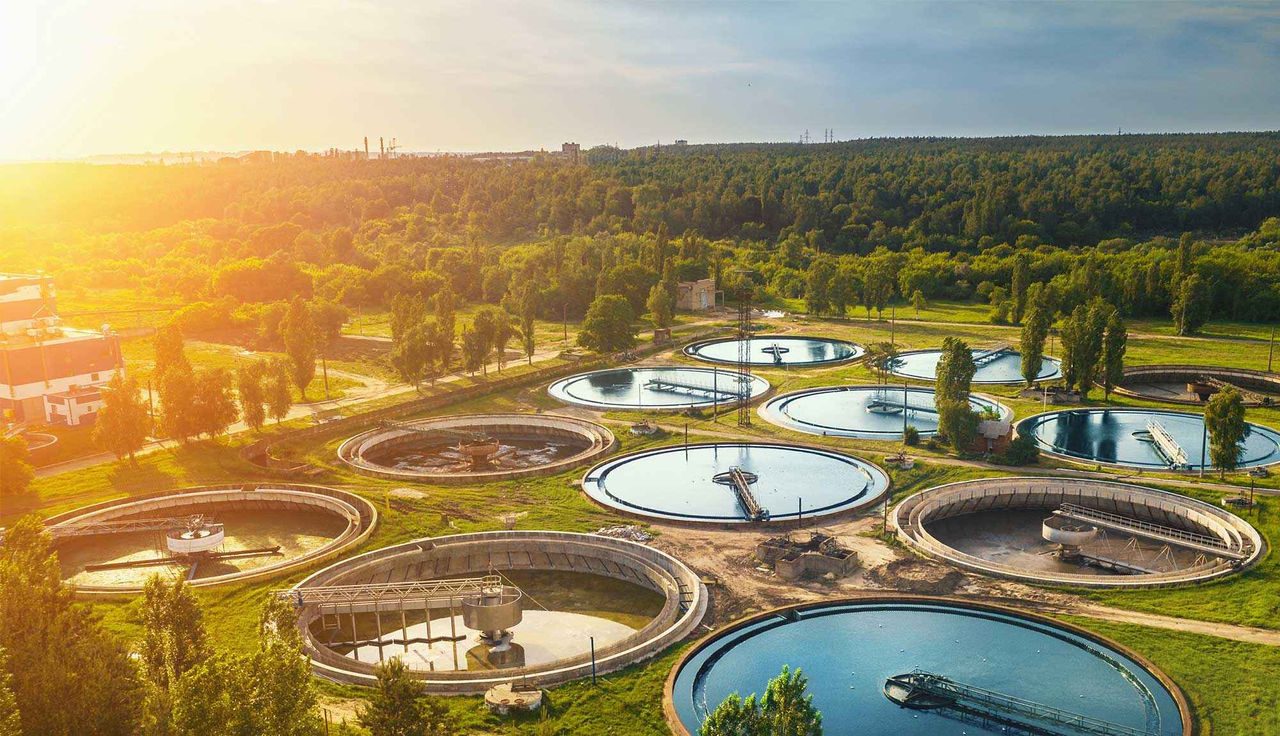
Filtration: Definition, function, and meaning for people, nature, and industry
The air we breathe, the water we drink, and many of the products we use daily undergo filtration processes. These processes remove harmful particles and impurities. This makes filtration a vital part of our world – indispensable not only for our health but also for the economy. The importance of filtration goes far beyond the technical definition of the process. What does filtration mean? Why is it important? Where does it take place, and how does the filtration of air and water work? We answer these and many other questions.
Filtration explained: How filters work and how they improve our lives
Filtration is a fundamental separation process that plays a critical role in our daily lives, safeguarding people, protecting the environment, and preserving machinery. At its core, filtration involves removing particulate contaminants from a gas or liquid by using a porous filter medium. This medium allows the gas or liquid to pass through while trapping contaminants such as particles.
The world of particles: Challenges in the filtration process
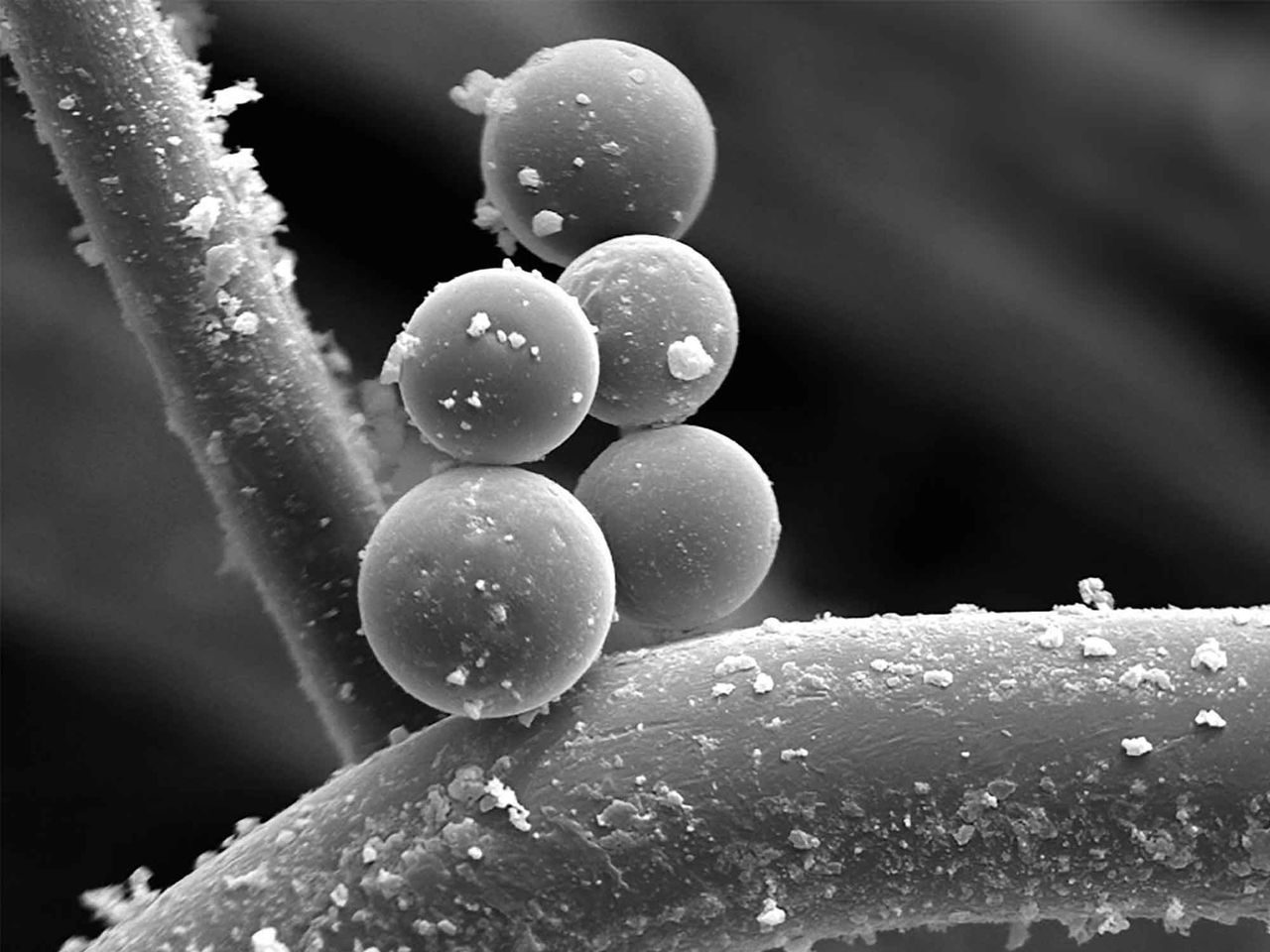
The core of the filtration process is the filter medium, where particles are separated. These particles can vary significantly in shape and size. From spherical to elongated, from regular to irregular shapes, their diversity is remarkable. Even the surface texture of particles can differ, ranging from smooth to rough. For better context, here are some examples of particle sizes (in micrometers):
- A human hair is 100 μm in diameter.
- A fine grain of sand is approximately 90 μm.
- Pollen grains have a diameter of < 15 μm.
- Fine dust particles can be smaller than 10 μm, and soot particles even less than 1 μm.
What are filter media and how are they structured?
Filter media are used to remove particles or pollutants from liquids or gases by trapping them while allowing the purified air or fluid to pass through. Fiber-based filter media, often made from synthetic or natural fibers, are commonly used and are characterized by a random fiber structure.
The right selection of a filter medium for a specific application depends on various factors. Key factors include the particle system, which is described by the particle size distribution, as well as the material (density) and shape of the particles. Additionally, the type of fluid and the volume flow rates play an important role in choosing the correct filter medium. The effectiveness of particle separation is determined by these factors, but primarily by the structure of the filter medium, which is optimally selected for the application.
Particle retention in filtration: How particles are captured
The goal of filtration is the removal of particles from the fluid, the so-called particle retention. This is a complex procedure that relies on various physical principles and can vary depending on the type of filtration and the properties of the substance being filtered.
Different types of filtration: Depth filtration vs. surface filtration
There are two primary mechanisms by which a filter medium captures harmful particles:
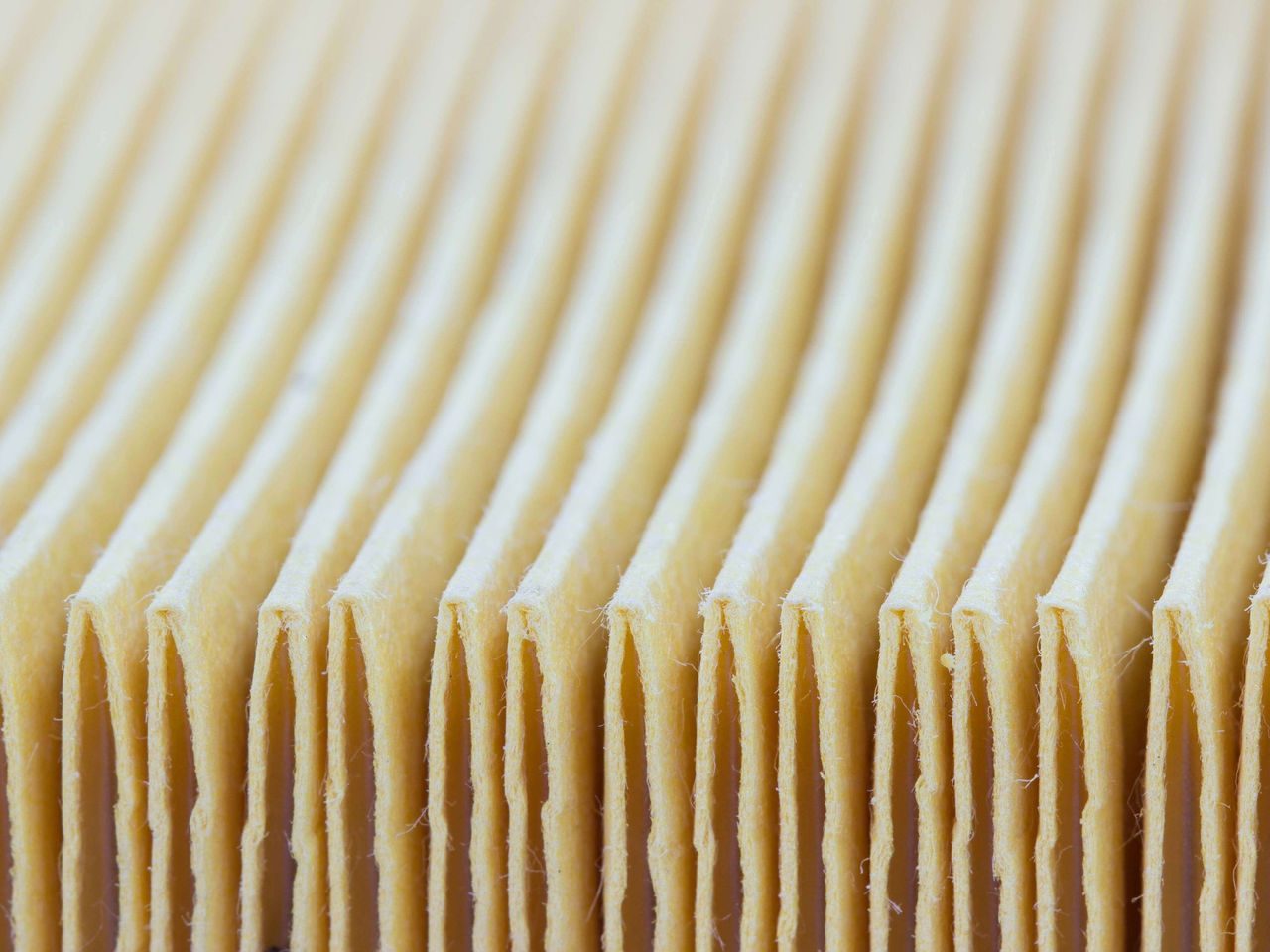
- The depth filtration captures particles throughout the entire structure of the filter medium. The fluid, whether liquid or gas, flows through a porous material where impurities are retained by mechanical, electrostatic, or adhesive forces. The particles are deposited within the pores of the filter material. This principle allows for a high dust holding capacity and effective filtration of fine particles.
- In the surface filtration, particles are retained on the surface of the filter medium, forming a "filter cake" – a layer of particles that acts as an additional filtration medium. For this reason, surface filtration is also referred to as cake filtration.
Most MANN+HUMMEL products initially operate using depth filtration. As the filter element accumulates contaminants, the larger pores within the filter medium gradually clog, leading to the formation of a dense particle layer. At this stage – known as the clogging point – depth filtration transitions into cake filtration, as the newly formed particle layer begins to function as a filter medium itself. In certain applications, this "filter cake" can be periodically cleaned using pulse-jet technology. This process involves short, powerful pulses of compressed air to release accumulated particles from the filter surface, maintaining optimal filtration performance. In other cases, the filter element reaches its end-of-life point, requiring servicing or replacement.
Filtration mechanisms: Capturing particles of different sizes
The different air filtration mechanisms can be explained using a simplified model of a single fiber within the fluid stream:
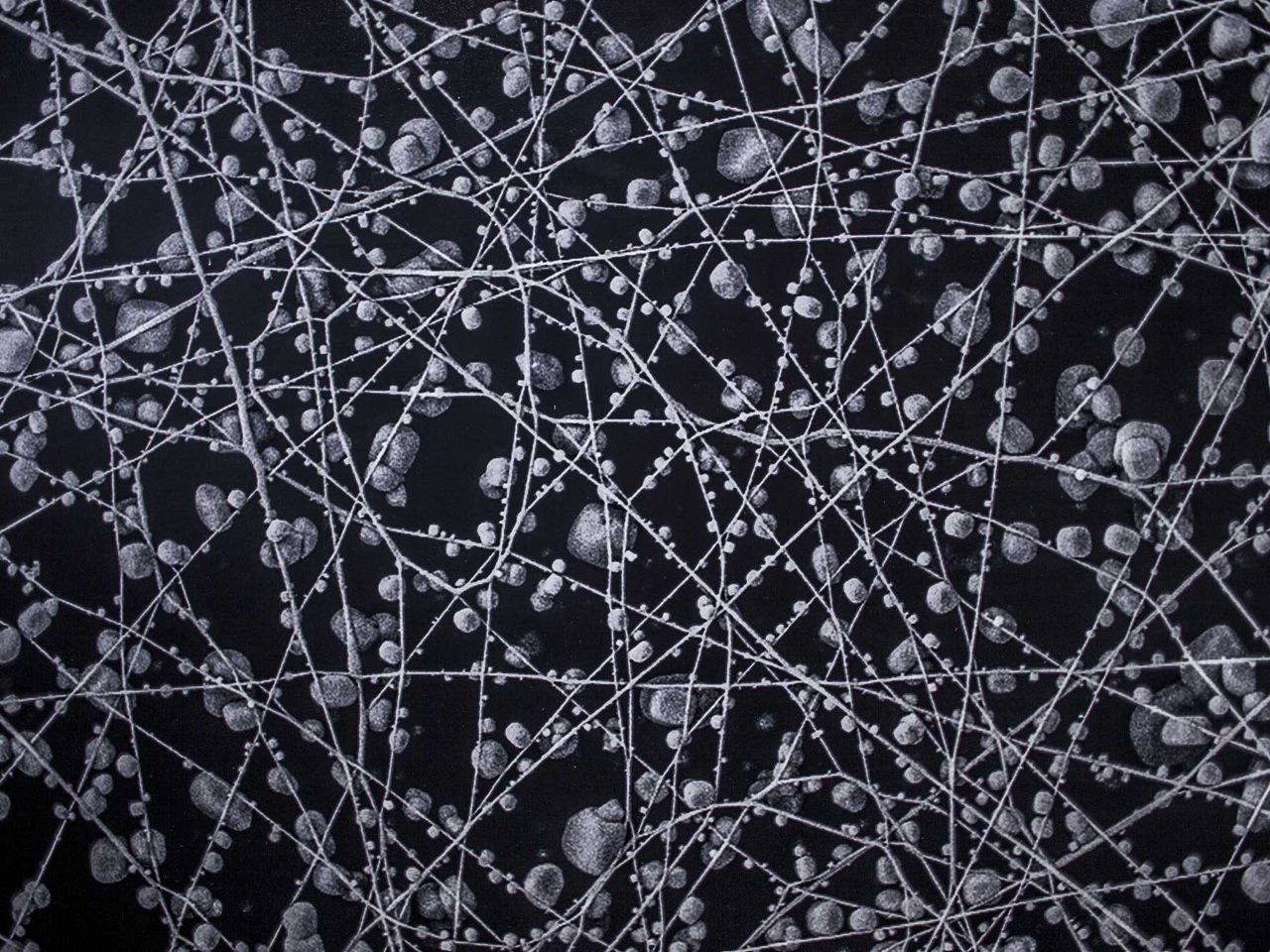
- Interception: Particles that closely follow the fluid’s streamlines may come into contact with the fiber due to their size and are subsequently captured. Larger particles are more likely to make contact.
- Inertia: Larger particles may be too massive to follow the fluid’s streamlines. Instead, they deviate from the flow and collide with the fiber, where they are retained.
- Diffusion: Extremely small particles move randomly due to diffusion and do not follow the streamlines. The smaller the particles, the more significant this effect becomes. This increases the likelihood of contact with the fibers, allowing them to be captured. This filtration mechanism is particularly effective at separating very small particles (< 0.1 μm) compared to larger ones.
Membrane technology from MANN+HUMMEL
Filtering groundwater, surface water, or wastewater requires a specialized approach: membrane technology. A membrane is an ultra-thin layer or barrier – either porous or non-porous – that selectively separates components in a mixture. While porous membranes rely on extremely fine pores, typically in the micrometer or nanometer range, non-porous membranes allow only individual molecules or ions with very small molecular sizes to pass through. This selective separation is based on the size, charge, or other physical and chemical properties of the molecules or particles. Membranes can be crafted from synthetic or natural raw materials, offering versatility in their applications.
The performance of membrane filtration is determined by the separation properties of the membrane. Filtration processes are classified into microfiltration, ultrafiltration, nanofiltration, and reverse osmosis. These methods provide energy-efficient and selective barriers against waterborne contaminants. Additionally, they are chemical-free, making water treatment more sustainable and safer. Their straightforward operation also facilitates use across a wide range of applications.
The filtration triangle: Balancing filter performance
The filtration triangle is a model that describes the three fundamental performance indicators of filter media:
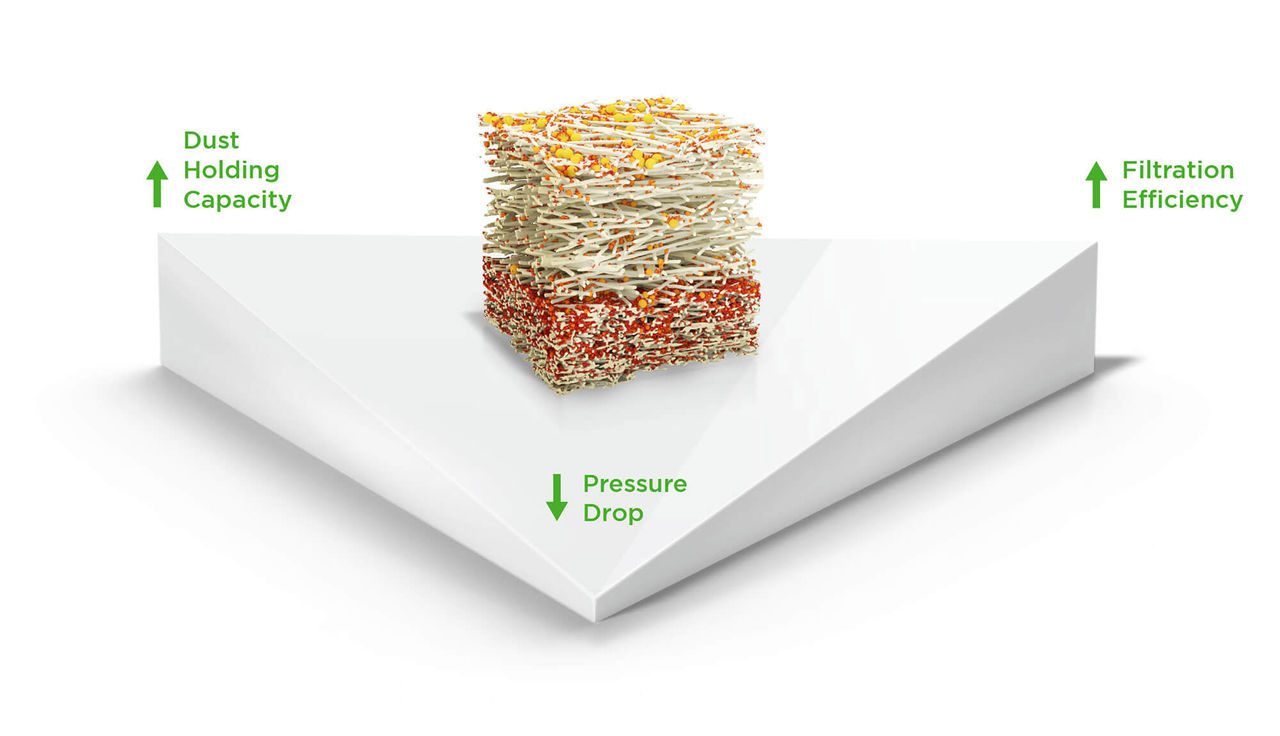
- Separation efficiency: The ratio of particles retained by the filter to the total number of particles entering it. For example, a separation efficiency of 99.9% means that only 0.1% of particles are not filtered.
- Differential pressure: This describes the flow resistance and correlates with the energy required to overcome the filter resistance.
- Dust holding capacity: The amount of particulate matter a filter can hold before exceeding the maximum allowable pressure drop.
These three factors affecting filtration performance are interdependent. Increasing separation efficiency often leads to a higher pressure drop, which in turn reduces dust holding capacity and shortens filter life. At MANN+HUMMEL, we find the best balance for each application, achieving the optimal compromise between separation efficiency, differential pressure, and dust holding capacity. This allows us to maximize filter lifespan while meeting the required efficiency.
Further challenges in filtration technology
Filter media must be robust and durable to withstand diverse applications and often long operating periods. Depending on their task and function, they face various challenges. For example, certain filtration solutions need to be temperature-resistant and/or mechanically and chemically stable.
This can be a decisive factor for the functionality of a filter. In some applications, filters must withstand temperatures ranging from -50°C to +350°C (-58°F to 662°F). For example, in internal combustion engines, oil filters must handle oil temperatures of up to 160°C (320°F). In the pharmaceutical industry, high-temperature HEPA filters may be exposed to temperatures as high as 350°C (662°F).
Applications in oil and fuel filtration demand high chemical resistance, which is often achieved by impregnating the filter media with phenolic resin. By contrast, air and cabin filters typically require lower chemical resistance but must maintain sufficient mechanical stability to perform effectively.
Therefore, when developing an appropriate filtration solution, various aspects must be taken into account.
MANN+HUMMEL filtration solutions: Maximum efficiency and performance
As a global leader in filtration technology with over 80 years of experience, MANN+HUMMEL offers a wide range of standardized and customized filtration solutions tailored to diverse industries and applications. Since 1941, we have specialized in separating the useful from the harmful across numerous fields, including:
- Automotive: Cabin air filters, oil filters, engine air filters, fuel filters, and urea filters.
- Pharmaceuticals: BIO-CEL membranes, HVAC systems, EPA, HEPA, ULPA, and molecular filters for ultrapure air and water.
- Food and beverage: TurboClean ultrafiltration (UF), nanofiltration (NF), and reverse osmosis (RO) solutions.
- Wastewater treatment: BIO-CEL MBR and RO membranes with advanced filtration technologies for gaseous and liquid waste separation.
- Household: Air filters for ventilation systems and household appliances, designed to optimize noise reduction, energy consumption, and filtration performance.
Filtration is an essential part of everyday life and industrial processes. It plays a crucial role in protecting health by purifying the air we breathe and ensuring the quality of the water we consume. At the same time, filtration ensures the efficiency and reliability of machines across countless applications. MANN+HUMMEL is dedicated to developing tailored solutions for cleaner mobility, cleaner air, cleaner water, and cleaner industries.
Contact us today for personalized advice and filtration solutions designed to meet your specific needs.